Mat
Controller
Common Design
Critera for both the
Metal Box and DIN-rail Safety Relay
Controllers
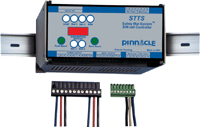
|
The STTS Mat Controllers
utilize the diverse redundant design
concept. When combined with the advanced
STTS Safety Mat System, the controllers
provide compliance with OSHA, ANSI, RIA,
CSA, and the European draft standards
EN954-1 and EN1760-1.
These standards dictate
safety of machinery and the related parts
of control systems and their
pressure-sensitive protective devices.
These standards focus on creating a fault
tolerant system.
|
Control Reliable
System—Critical
components are duplicated so a single component
failure will not cause an unsafe condition. If
a component does fail, the self-checking
circuitry recognizes the fault and initiates a
safe stop of the machine. The fault is then
displayed on the message
display.
Self-Checking
Circuitry—The STTS Mat Controller
will self-check every 20 milliseconds.
Self-checking is the ability to
electronically verify that all of the
system's critical internal circuit
components and their redundant
counterparts or back-ups are operating
properly.
|
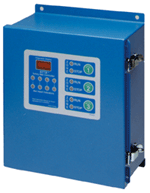 |
Diverse Redundancy Design
Concept—The STTS Mat Controllers utilize the
diverse redundancy design concept. This gives the mat
system a higher level of redundancy and control
reliability. The two microprocessors are of different
design, and the microprocessor or parallel programs are
programmed from different instruction sets written by
different programmers.
Redundant Captive Contact Safety
Relays—Redundant relays assure safety should an
output relay fail. The STTS Mat Controller utilizes
safety relays which have force-guided contacts. This is a
configuration where the contacts are mechanically locked
together so if one set of contacts weld, the other
contacts cannot change state.
Alphanumeric Diagnostic Message
Display—Scrolling message display shows status and
fault codes. This is an excellent safety and maintenance
feature unparalleled in the machine guarding industry for
increasing uptime.
Circuit
Description—Low voltage DC signal (+/- 20VDC) is pulsed
to the mat simulating a 24VAC signal through two wires.
The wires are attached to the top and bottom electrodes
(internally) of the mat. Force on the mat lowers the
resistance between the two wires causing a drop in
voltage. A second pair of wires coming back from the mat
is used to sense this drop in voltage. The redundant
circuits compare the voltage to a reference and shut down
the zone when the voltage drops below the reference. The
circuit goes through a self-check to verify that the
reference, comparators, mat, wiring, and other circuits
are all functioning normally every time it scans a mat
input. Diverse redundant technology, provided by two
different computers, controls the whole system and
provides a higher level of safety and system
flexibility.
The following standard provisions
are designed into both mat controllers to facilitate the
guarding system interface and monitoring desired (usage
is optional):
External Relay Check
Provision—The External Relay Check allows the STTS
Mat Controller to monitor a pair of external relays in
series using the external relays secondary set of DRY
contacts, provided they are N.C. force-guided contacts.
The captive or force-guided contacts will maintain the
identical position as the primary set of contacts on the
external relays, except the secondary set of contacts are
wired to signal the reverse of the primary (i.e., primary
contacts are N.O. and secondary contacts are N.C.). The
circuit looks for both closing and opening of the
external relay contacts. The STTS Mat Controller provides
a safe external relay check.
Application—Monitoring external relay contacts for
shorts, opens, or welded contacts.
Auxiliary Output Contact
Provision—The Auxiliary Output contact provides a
N.O. or N.C. isolated (DRY) contact output to signal the
condition of the mat system. The output is used in
conjunction with the standard pair of output relays that
are wired to the safety circuit of the equipment.
Application—Signal to PLC, etc.
DeviceNET™
Complete system
monitoring on DeviceNET™ fieldbus networks. The STTS Mat
Controller family if fully compatible with the DeviceNET™
fieldbus and can be connected directly into the fieldbus
for non-safety monitoring of system status. DeviceNet™ is
the leading low cost communications link that connects a
wide range of automated manufacturing devices for greater
usability and convenience. Multiple STTS Mat Controllers
can be networked with numerous other devices on a single
DeviceNet™ network. Add suffix DN to controller part number for
this optional feature.
|